Process control: why it is important and how can it improve your business?
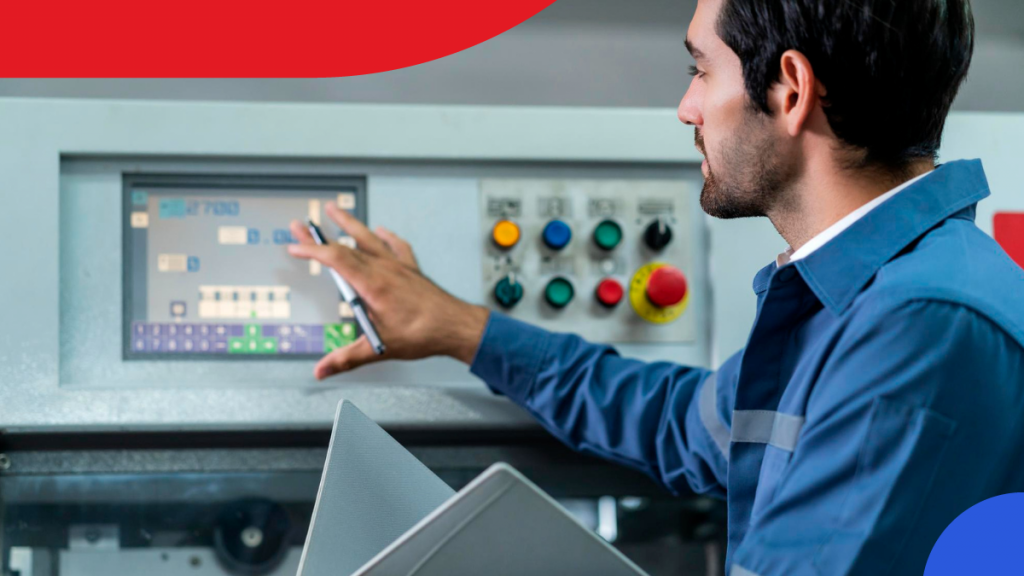
Conteúdo
Process control is essential for managers who seek to improve the results of their companies by optimizing resources and increasing productivity.
This is fundamental for achieving a competitive edge in the market. By taking the most important strategy to the next level, namely offering an enchanting experience and excellent customer service, companies can solidify their position.
To emphasize the importance of this subject, a recent survey revealed that 54% of customers feel neglected by companies, prioritizing those that care genuinely about their experience.
Process control enables continuous improvement, as well as a better allocation of the organization’s financial and human resources; reducing failures and standardizing activities and operations.
If you are seeking further information on the subject, you have come to the right place. In this post we will discuss what process control is, as well as how to implement it effectively in your business. Good reading!
What is process control?
Process control involves creating, analyzing and improving the methods used across all departments of a company; optimizing results, reducing costs and improving management as a whole. Its primary objective is to increase the organization’s profitability.
By implementing it, companies can adapt swiftly to market opportunities and threats, generating more value for the customers and identifying business activities that are not aligned with the established goals.
Process control goes beyond prevention, it also focuses on error recurrence and standardization. Its aim is to foster continuous improvement within the enterprise.
Check out 5 ways to enable process control with process mining:
Why is process control important?
Process control is crucial for companies aiming to establish standardization in the quality of products and services offered to its customers, thereby strengthening their brand reputation.
McDonald’s is an excellent example. Regardless of the branch visited, the quality of the product remains consistently high. For this to happen, there is a strict process control within the restaurant chain.
The big difference is precisely the level of standardization. Therefore, when effectively implemented, process control helps managers to better define roles and responsibilities, identify faults in real time, and create continuous improvements.
What is the purpose of process control?
The primary purpose of process control is to optimize systems and workflows, thereby improving the company’s overall performance to achieve the strategic objectives set by its managers.
This allows the organization to adapt more easily to emerging consumer demands.
Technological resources and industrial automation are key tools employed in pursuit of this aim. The result is an increase in productivity, as well as an improvement in the quality of products and services.
Through effective process control, managers can monitor the progress of activities and make decisions based on real indicators.
Check out the difference between processes and projects:
What are the benefits of process control?
The greatest benefit of process control is delivering products faster and with higher quality to consumers. In addition, it allows managers to reduce costs at all stages in an organization.
In summary, process control provides:
- Increased productivity;
- Cost reduction;
- Quality improvement;
- Greater standardization.
Increased productivity
By eliminating rework, production time at any stage is reduced, resulting in increased productivity.
Furthermore, automation enhances employee efficiency and reduces errors, as it offers more security for all collaborators involved.
This means that there are more deliveries in less time.This not only benefits the company but also enhances customer satisfaction through greater efficiency.
Here are some other essential tips to increase your productivity:
Cost reduction
By eliminating rework, costs are reduced and employees’ time is better utilized for other activities, resulting in savings for the company
Additionally, effective process management leads to a reduction in direct product costs in direct production line processes.
For example, if a product that used to take one hour to produce can now be made in 54 minutes, resulting in a 10% reduction in production time and a corresponding 10% reduction in fixed costs.
Quality improvement
As process control minimizes human error, there is an improvement in the quality of products and services provided and fewer errors are passed on to the product. For instance, in the context of industrial processes for producing t-shirts, good process control ensures that the product reaches the consumer without any flaws in the cut, enhancing overall quality.
Greater standardization
Another advantage of process control is the increased standardization in the execution of activities; even when personnel changes occur within a department,work is not compromised.
The predefined processes facilitate the understanding of responsibilities for all individuals involved, ensuring continuity and consistency.
Read also:
- Do you know about strategic planning? Find out by answering these 3 questions
- What are stakeholders: 5 tips for good stakeholder management in your business. Their definition, types and importance
What are the process control types?
Several types of process control support decision making, ensuring the continuous improvement of workflows, as well as the company’s deliveries. Some of the main types include:
- Process mapping;
- BPM;
- Statistical process control.
Process mapping
Process mapping is the design of all the company’s work flows, graphically identifying the interactions and responsibilities of each department.
This map enables discussions on alternative approaches to improve the workflow and deliver the service with greater agility and quality.
Mapping control allows managers to identify problems and opportunities for further improvement of greatest tension points, as well as in the most flawed processes.
In other words, it transmits the information, clarifies roles and responsibilities, guides the definition of goals and creation of KPI’s and helps to improve process control.
BPM
BPM (Business Process Management), encompasses a set of techniques that improve the processes involved in delivering a product or service.
By aligning processes with strategic goals, BPM enables teams to work in harmony and achieve continuous improvements, ultimately enhancing customer perception, optimizing time and resources, and aiding decision-making.
Statistical process control
Statistical control allows managers to identify workflow failures, which is a crucial tool in process control.
After all, it is through indicators that managers measure and identify processes that are misaligned with the company’s goals.
It allows for in-depth analysis of the causes of problems, enabling managers to develop strategies to prevent their recurrence.
How to control processes?
Any manager can implement process control following these five steps:
1. Map the processes
Design and document the entire flow of activities within the company using techniques like process mapping, which provides a graphical representation of the workflows, roles, and responsibilities.
It is through the flowchart that it will be possible to understand which people are involved in each of the stages, and determine the desired direction for the company.
A method used in this phase is the BPMN notation, a graphical representation with a language that is easily comprehensible to all collaborators.
As a result, managers create documentation for standardizing processes.
2. Process automation
With the help of an effective system, it is easier to optimize the standardization of your company’s processes. It is even possible to make them automatic, which avoids errors, reduces costs and facilitates the work.
In addition, the platform centralizes information, making it accessible to all employees and stakeholders in real time. Automation extends beyond production processes to administrative, financial management, inventory control, or human resources.
3. Determine the KPIs
Improving processes is simply not possible without understanding them deeply. And the best way to do so is through performance indicators.
It is important to understand that process control can only be carried out based on real data, otherwise it will not be possible to compare the documented processes. Use the following indicators:
- Time;
- Quality;
- Financial feedback;
- Productivity;
- Compliance with the strategy.
The more indicators you extract from your business, the more knowledge you will have about the company’s processes, enabling even more improvements.
4. Monitor team performance
Once the indicators are defined, it is necessary to monitor them. Continuously monitor KPIs to identify faults, make timely corrections, and ensure alignment with strategic objectives. This focus on continuous improvement enhances competitiveness and productivity.
5. Update the mapping
Since processes can change, it is necessary to regularly update process maps.
New indicators can be developed as processes evolve over time.
The importance of a process control system
To effectively control processes, having a robust system is essential, especially for larger organizations with complex processes and data.
Therefore, a system provides more security and accuracy in monitoring, as the processes are mapped, modeled and executed within a platform.
As a result, there are fewer losses and human errors; process control is faster, allowing the organization’s strategic objectives to be achieved much more easily.
A good system allows access from anywhere, enabling managers to stay connected to their team’s performance even when physically absent from the company.
How does a good system support process control?
A leading edge system supports process control in all its stages, such as mapping, execution, monitoring, analysis and process management, with focus on continuous improvement.
Therefore, having an effective system at his fingertips, the manager can:
- Better delegate tasks;
- Determine rules and KPIs to measure processes performance;
- Document activity flows;
- Continuously improve processes.
In other words, a good system is the necessary parameter to ensure more effectiveness when implementing process control within the company.
How to choose a process control system?
To find an effective process control system, you first need to map your business activity flows. This step provides a clearer outlook for your specific needs.
Based on them, you can explore various software options on the market that automate your organization’s processes, improving the performance of the entire team.
An indicator software that deploys your business strategies, connecting projects, executing action plans, and delegating tasks in one place is STRATWs One, by Siteware.
This innovative software serves as an indicator tool, facilitating the deployment of your business strategies by seamlessly connecting projects, executing action plans, and effectively delegating tasks, all within a unified platform. Interested? Request a free try out: