7 principles for successful quality management in business
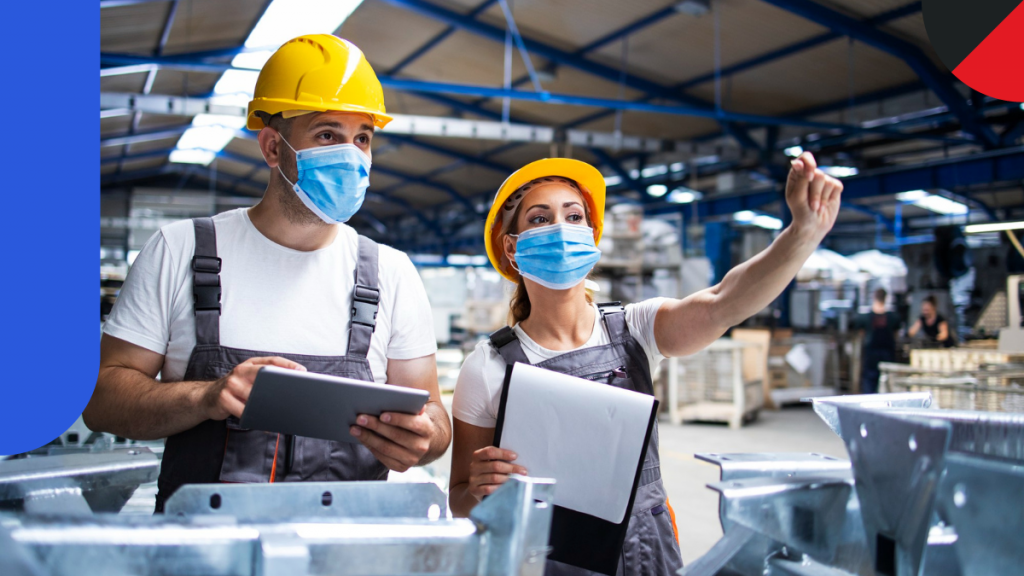
Conteúdo
Quality management is a key activity for organizations that need to deal with today’s highly competitive business scenario, provide a customer-focused culture and boost client satisfaction.
After all, it’s impossible to talk about customer success without mentioning quality management; that is, the act of overseeing a company’s strategic operations as a whole, identifying unnecessary processes and delivering a favorable customer experience.
Keep reading and find out more about how quality management works and the principles you need to apply for a more successful business management strategy.
The PDCA Cycle is a tool that works on business continuous improvement. Read more about it on: What is the PDCA Cycle and how can it improve your business processes?
What is quality management?
Quality management is the act of supervising an organization’s processes and tasks that are directly involved in product development. This aims to meet customer’s demands and standards.
Also, it provides inputs for a more assertive strategic planning focused on a customer-focused culture.
There is not a specific way to implement quality management in business. Any decision made to improve the organization can be considered as such.
The 4 components of quality management
Although there is no magic trick to apply quality management, there are 4 essential elements to take into account for it to be effective:
- Planning;
- Control;
- Improvement;
- Assurance.
These requirements are part of a process known as Total Quality Management (TMQ).
Vale dizer que o gestor precisa estar atento pois a gestão de qualidade não deve se concentrar apenas nas saídas dos produtos e serviços, mas também nas entradas e nos processos pelos quais as saídas foram criadas.
This means that the implementation of these elements must help to oversee the whole product and service development and delivering —from beginning to end.
What are the main quality management goals?
The main objective of an effective quality management project is to create a continuous improvement plan within the organization. The goal is that products and services not only meet, but also exceed customer expectations. Companies must constantly pursue quality in order to keep being competitive.
In this context, quality management not only ensures customer satisfaction, but also provides the employee’s well being, once it minimizes operational mistakes and keeps the workflow running smoothly.
Also, managers must understand that an effective quality management demands seeing beyond the product development processes.
At the same time, the organization’s culture must stimulate a quality mindset to improve performance throughout the productive process. Thus, everyone is linked by the same objective: operations effectiveness, cost reduction and high-quality competitive products.
The DMAIC Cycle can also be used to apply quality management in business. Learn how on: What is DMAIC and how to use it?
What’s quality management’s role in a company?
Quality management’s main role is gathering all available business resources –technology, human capital, tasks and strategies– in order to provide the best customer experience.
Managers must guarantee that each member of the organization understands the importance of the system and is engaged in the processes.
Also, they must narrowly oversee tasks and operations in order to customize standard processes, tools and frameworks. Gradually, it’s possible to identify quality standards for every process –não matter how big or small– and also to eliminate bottlenecks.
Tech systems are good allies to operation’s control, as software allows transparent real time performance visualization that provides better insights for decision makers.
What are the benefits of quality management?
A good quality management system is a mandatory investment to improve business competitiveness. In addition, it brings a lot of other benefits.
The first and most important one is the significant improvement throughout your business —from employees’ hiring processes to product delivery. Other advantages are:
- better efficiency;
- cost-cutting and less human error;
- consistent results;
- enhancement of team skills;
- agile onboarding and new employee’s training.
What are the principles of quality management?
According to ISO 9001, these are the 7 principles that better describe a quality management system:
- Customer focused;
- Leadership;
- Continuous improvement;
- Team engagement;
- Evidence-based decision making;
- Processes management;
- Relationship management.
Each one of them is essential to develop and execute more effective, assertive and consistent practices.
- Customer focused
Companies must put customer success as one of their goals; so every plan and action results in client satisfaction.
In order to do so, the team must identify customers’ needs and pain points to meet and even exceed client’s product or service expectations.
- Leadership
Leadership is essential for quality management in any organization. Great leaders know how to encourage the team to pursue the company’s common goals.
It’s up to them to ensure that every process will follow the business’ quality standards, and also to prevent any bottleneck from hindering the operational flow.
- Improvement
No business suddenly reaches perfection from one day to the next. That’s why processes must be often improved in order to respond to customer’s needs.
This kind of culture reaches out to all team members and promotes continuous upgrading for a more competitive business.
- Team engagement
People engagement is another relevant principle of quality management. It focuses on integrating members and stakeholders in order to achieve full quality.
Total engagement throughout the organization ensures that managers are able to constantly implement improvements to products and services.
Investing in an employee’s professional training is essential to upgrade processes and provide a successful customer experience.
The Human Resources department is responsible to keep every employee engaged in the organizational culture.
- Evidence-based decision making
A data-driven process management is also important to provide evidence-based decisions and to improve quality standards.
A manager must chart business procedures in order to extract metrics and KPIs from every stage of the production process. Thus, it is possible to monitorate the results and evaluate if the strategy is really going well.
- Process management
Quality Managers should have a systemic view over business processes in order to implement quality standards every step of the way.
It allows to identify and understand the relationship between each stage of the product development process and make adjustments when necessary.
Therefore, companies need to qualify their managers so they get proper knowledge about this systemic approach.
- Relationship management
Another keystone of quality management systems is the relationship between collaborators, suppliers and other strategic partners. They must work together to perform quality procedures in any sphere of the organization.
Proper training is essential to integrate teams and promote best customer success practices.
Also, assertive business communication and efficient networking skills are crucial for managers and CEOs delivering valuable services and products to their clients.
Why is quality management important?
Businesses that implement a quality management system improve processes and routine operations significantly.
A rigid quality control allows managers and team members to achieve better results and apply all 7 principles.
Quality management also helps to:
- increase productivity;
- perform processes statistical control;
- optimize resources;
- achieve customer success.
Increase productivity
Minimalizing jams and mistakes speeds and secures the operational workflow, which leads to more efficient daily processes.
Also, a systemic management provides qualified metrics and KPIs to correct eventual problems faster. Therefore, the positive impact reaches out to the whole team —from the back to the front-office.
Perform processes statistical control
A good quality management system also offers teams a wide overview of operational processes.
Thus, it makes it easy to monitor problems in real-time and deliver products under business quality standards.
Optimize resources
The quality management system impacts the whole organization. For instance, it optimizes resources for stock flow, which guarantees better use of resources.
Well defined guidelines help teams to effectively manage the available resources in order to reduce waste and, therefore, minimize costs.
Achieve customer success
Productivity increase and resource optimization provide more agility and high-quality standards in product delivery. The result is a better customer experience.
Workflow jams and production mistakes means the company loses time and money to solve everyday problems. As a result, orders get delayed and customers get unsatisfied with the brand.
High rates of customer success will probably ensure a long-term relationship between a business and their clients.
How technology makes a difference in quality management?
Software is key to implementing quality management in your business. It gives you the right tools to visualize your operational status and make the best strategic decisions.
STRATWs One monitors processes in real-time, standardizes management methods, and follows team development at every stage.
As a result, the company corrects bottlenecks and continuously improves the product development process —from feedstock arrival to product delivery.
Request a free demo!