What is an Ishikawa Diagram and how do you create one?
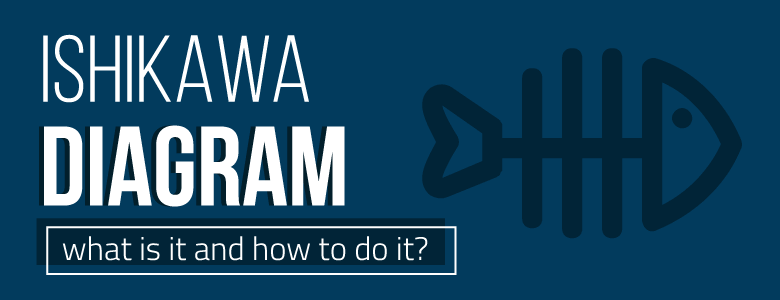
Conteúdo
What is an Ishikawa diagram?
The Ishikawa Diagram is a tool intended to help a team get to the actual causes of problems in processes. In other words, its purpose is to find out which factors result in an undesired situation in an organization.
It was created by Chemical Engineer Kaoru Ishikawa in 1943, and may also be referred to as cause and effect diagram, fishbone diagram or 6M. Those names refer to the goal, shape and categories of the method itself.
As it is a visual tool, the fishbone Ishikawa Diagram is widely used to help team organization and reasoning. By means of its graphic representation, it helps a team get to the root causes that decrease productivity in an organization.
What are the benefits it brings to an organization?
The diagram, a graphic, simple to build and easy to understand representation, brings several benefits to an organization and to the team using it, some of which are as follows:
- Better perception of problems;
- Identification of possible causes;
- Ranking the causes found;
- Visual record making future analyses easier;
- Process improvement;
- Exploring ramifications of problems;
- Involving the whole team in quality management;
- Group idea organization.
The Ishikawa Diagram brings a lot of benefits to companies, when put to good use. It may be used in conjunction with other methodologies, such as brainstorming meetings, which potentiate meeting output and help the team to present their ideas and points of view.
Therefore, it is important to take some limitations and requirements into account for its proper use. For instance, the method on its own does not identify how serious causes are. In addition, it needs people who are organized, who know how to coordinate meetings, and who have leadership characteristics, to deploy the tool.
How do you use an Ishikawa Diagram?
You have already noticed how it may be useful, so let’s learn how to create one! Follow the steps below:
- Define the problem to be analyzed by the team;
- Draw a horizontal arrow pointing right and put a square at the end of it;
- Write your core problem inside that square;
- Draw diagonal lines long the arrow extension, which will be the categories of your causes found;
- Brainstorm with your team to define possible causes. This is the longest and most demanding part of the method, thus, it is important to focus on your details, so as to get it done right;
- Within the categories defined by the team, enter the causes found; You may list them according to their seriousness or relevance. A good tool to help that ranking process is the Prioritization Matrix.
To create the categories in step 4, you may create your own, in keeping with each specific requirement. You may also follow 6M logic, which are the original categories in the method:
Method: how does the way the work is performed impact the problem?
Machine: how does equipment used in the process impact the problem?
Measurement: how do the metrics used to measure activity progression impact the problem?
Mother Nature: how does the environment where the activity is performed impact the problem?
Material: how do quality and type of materials used impact the problem?
Manpower: how do people involved in the activity impact the problem?
Conclusion
One of the most common mistakes companies make is letting small problems and failures interfere with their processes, without going deep into or fighting their causes. That eventually deteriorates routines, leading to losses and making the company less and less productive.
As one of the most important tools for quality management, using the Ishikawa Diagram helps keep those activities at constant improvement, and make your problems easier to solve, from the simplest to the most complex ones.
It is a multipurpose, easy-to-understand and easy-to-view tool, improving team understanding of all processes. Additionally, it may be used throughout all departments in organizations, thus, investing in that kind of management is one of the ways to success!
When using the Improvement Opportunities in our strategy execution software, you have total access to the Ishikawa Diagram and other advanced problem analysis and solution tools. Thus, you can better spot organizational failures and sort them out in an effective way.
Revolutionize the management of your company with STRATWs One